Comparative Lifecycle Assessments:
Lead and Lithium-Iron Phosphate Batteries
Major manufacturing industries rely on lead-based batteries and lithium-iron phosphate batteries for critical energy storage. Each has advantages. Yet, comparing the two technologies shows quite different sustainability profiles, particularly during their manufacturing phase.
Lead Battery Sustainability Surpasses Lithium-Iron Phosphate in Manufacturing
Comparative lifecycle assessments between certain lead-based (Pb) batteries and lithium-iron phosphate (LFP) batteries have made an important conclusion: Lead battery sustainability substantially surpasses lithium-iron phosphate in manufacturing.
The need to reduce global warming has made sustainability a key criterion in selecting energy storage technologies. Increasingly, the automotive, material handling and industrial sectors are factoring in a battery chemistry’s green profile during manufacturing – not just end-of-life recycling – in addition to safety, reliability and cost-efficiency. Lead batteries especially excel in modeling a successful circular economy.
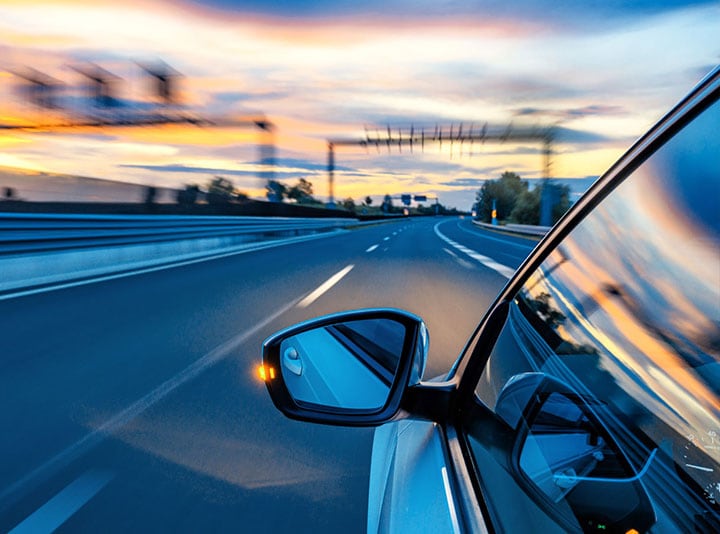
Manufacturing Impact: Comparing Automotive Batteries
Auto manufacturers of ICE, start-stop and micro-hybrids face new and emerging battery options. Many have an unknown impact on global warming. A comparative lifecycle assessment evaluated a 12V lead-based battery (Pb or PbB) and a 12V lithium-iron phosphate battery (LFP, also known as LiB-LFP).
- Key Finding The environmental impact of manufacturing a motive Pb battery is three times less than manufacturing a similar LFP battery.
- Global Warming Potential (GWP) is the most commonly used metric for quantifying the ability of each greenhouse gas to trap heat in the atmosphere. Manufacturing Pb batteries has a lower GWP impact than LFP batteries, under the assumptions taken in the baseline scenario of the study.
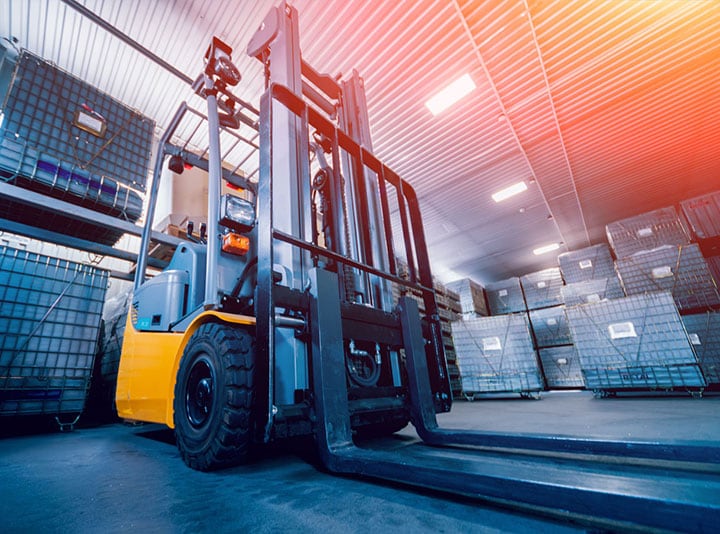
Manufacturing Impact: Comparing Motive (Forklift) Batteries
Experts predict that global demand for motive batteries will increase by over 63%, from 41 GWh in 2022 to 67 GWh in 2030. The material handling sector is rapidly replacing gas-powered internal combustion for forklifts to electric models with on-board power supply. This is driving demand for both Pb batteries and LFP batteries. A comparative lifecycle assessment evaluated the batteries, each were 48V, 500 Ah (24kWh).
- Key Finding The environmental impact of manufacturing a motive Pb battery is three times less than manufacturing a similar LFP battery.
- Global Warming Potential Manufacturing Pb batteries has a lower GWP impact than LFP batteries, under the assumptions taken in the baseline scenario of the study.